14 Cost-Saving Measures for Tracking and Managing Inventory Costs
Discover the cutting-edge strategies for reducing inventory costs with valuable insights from industry leaders. This article delves into practical solutions that streamline inventory management, from AI-powered tools to just-in-time systems. Experts weigh in on how to leverage technology and data analytics to optimize inventory efficiency and slash expenses.
- Leverage Data Analytics for Demand Forecasting
- AI-Powered Tools Optimize Eco-Friendly Inventory
- Just-in-Time System Reduces Excess Stock
- Predictive Software Anticipates Seasonal Demand Spikes
- Real-Time Tracking Supports Efficient Inventory Practices
- Centralized System Prevents Shortages and Overstocking
- JIT Approach Minimizes Waste in Training
- Software Adoption Streamlines Inventory Management Process
- Data-Driven Forecasting Enhances Inventory Efficiency
- Cycle Counting Maintains Accuracy Without Disruption
- ABC Analysis Prioritizes High-Value Inventory Items
- Vendor-Managed Inventory Reduces Overhead Costs
- Cross-Docking Cuts Storage Expenses Significantly
- RFID Technology Automates Inventory Tracking
Leverage Data Analytics for Demand Forecasting
One effective strategy we used at my previous work to manage inventory and minimize waste was demand forecasting powered by data analytics. By analyzing historical sales data, seasonal trends, and market patterns, we accurately predicted future demand and adjusted our inventory levels accordingly.
For instance, we utilized inventory management software like NetSuite or TradeGecko to automate this process. These tools integrate sales, supply chain, and market data into a centralized dashboard, enabling us to identify slow-moving products and optimize reorder points. As a result, we avoided overstocking items that may lead to waste and stockouts that disrupt customer satisfaction.
In practice, demand forecasting helped us reduce excess inventory by 20% while ensuring product availability for peak seasons. This not only lowered storage costs but also aligned our stock levels with real-time consumer demand, supporting sustainability goals by minimizing unsold goods.
This proactive approach enables better decision-making, reduces waste, and enhances operational efficiency, creating a balance between supply and demand.
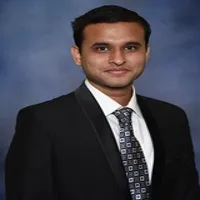
AI-Powered Tools Optimize Eco-Friendly Inventory
Effective inventory management is crucial for minimizing waste, especially in a sustainability-focused business. One key strategy we use is an AI-powered demand forecasting tool that helps us predict customer demand with high accuracy. This tool analyzes historical sales data, seasonality, and external factors like local events or weather, allowing us to adjust inventory levels proactively.
For example, we used this system to optimize the stock of our eco-friendly packaging products. By predicting fluctuations in demand during peak seasons, we reduced overproduction and waste by 21%. The tool also helps us avoid understocking, ensuring that we can meet customer needs without excess inventory.
In addition to demand forecasting, we implement a just-in-time inventory model, which minimizes storage time and reduces the chances of products becoming obsolete. This combination of technology and strategy has significantly improved our waste reduction efforts and aligned with our commitment to sustainability.
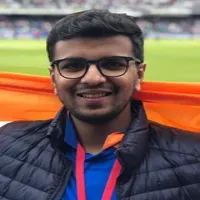
Just-in-Time System Reduces Excess Stock
Effective inventory management at 3ERP hinges on real-time tracking and demand forecasting. One strategy that has been especially impactful is implementing a just-in-time (JIT) inventory system. By closely aligning inventory levels with current production needs, we reduce excess stock and minimize waste from obsolete materials. For instance, instead of stocking large quantities of raw materials, we collaborate closely with suppliers to schedule deliveries based on project timelines.
This approach is supported by our ERP system, which integrates production schedules, sales forecasts, and inventory data, giving us clear visibility across the supply chain. While JIT requires careful planning and strong supplier relationships, it has significantly cut down on storage costs and material wastage, enabling us to operate more efficiently and sustainably.
Predictive Software Anticipates Seasonal Demand Spikes
At Pheasant Energy, effective inventory management revolves around data-driven forecasting and real-time tracking. One strategy that has worked well for us is implementing inventory management software with predictive analytics. This tool helps us anticipate demand fluctuations based on historical trends, ensuring we stock just the right amount of materials for our energy projects.
For example, during a recent project, the software alerted us to an upcoming seasonal spike in demand for specific components, allowing us to adjust our orders and avoid overstocking. By maintaining optimal inventory levels, we minimize waste, reduce storage costs, and ensure resources are available when needed. The key takeaway is that leveraging technology to align inventory with actual demand not only cuts waste but also boosts operational efficiency.
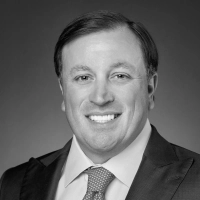
Real-Time Tracking Supports Efficient Inventory Practices
At ACCURL, effective inventory management starts with real-time data tracking through an integrated inventory management system. One key strategy we use is demand forecasting, leveraging historical sales data and market trends to predict inventory needs accurately. This approach helps us avoid overstocking materials, which ties up capital, or understocking, which disrupts production schedules.
For instance, implementing just-in-time (JIT) inventory practices has significantly reduced waste by ensuring we only order materials when they're needed. This strategy not only minimizes excess inventory but also streamlines operations, reducing storage costs and ensuring fresh, high-quality inputs for production. By coupling technology with predictive analytics, we've optimized inventory management to support efficiency and sustainability in our business.
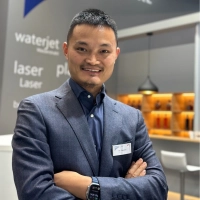
Centralized System Prevents Shortages and Overstocking
At City Storage, our go-to tool for tracking office inventory and supplies is a centralized inventory management system integrated with our facility operations software. This system allows us to monitor stock levels in real-time across multiple locations, ensuring that we maintain optimal inventory levels without running into shortages or overstocking.
The system prevents shortages by setting automated low-stock alerts, prompting reorders before supplies run out. It also avoids overstocking by tracking usage trends and recommending appropriate order quantities based on historical data. One key feature that makes it stand out is its ability to generate detailed reports, allowing us to analyze supply patterns and make data-driven decisions. This level of visibility and control has been essential in keeping our operations smooth and efficient.
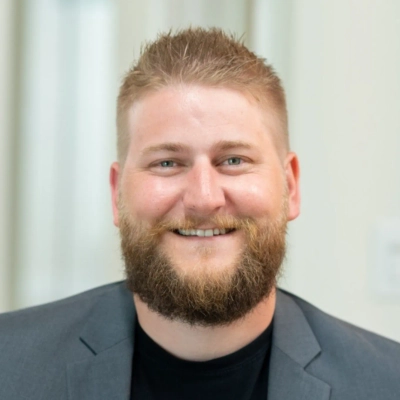
JIT Approach Minimizes Waste in Training
At Best Diplomats, managing inventory effectively ensures smooth operations for our training programs and resources. One strategy we use to minimize waste is just-in-time (JIT) inventory management.
This method allows us to order supplies and materials as needed, which helps us avoid overstocking and reduces the risk of expired or unused inventory.
A critical tool that supports our JIT approach is inventory management software like TradeGecko (now QuickBooks Commerce). This platform helps us track inventory levels in real time, monitor usage trends, and automate reordering processes based on demand forecasts.
By syncing our inventory data with our operational needs, we can ensure we always have suitable materials—office supplies or resources for training sessions—without holding excess stock.
This system has helped us significantly reduce waste by ensuring that we only purchase what's needed for upcoming programs. Additionally, it allows us to identify slow-moving items so we can take proactive steps to use or discount them, preventing them from going to waste.
By using JIT and inventory management tools, we optimize our spending and keep operations efficient, which is essential for maintaining both cost-effectiveness and sustainability.
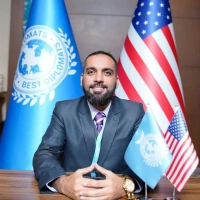
Software Adoption Streamlines Inventory Management Process
Managing inventory costs effectively is crucial for maintaining the profitability of a business. One common approach is using inventory management software that automatically tracks stock levels, sales patterns, and reorder points. This technology helps in reducing manual errors and improves the accuracy of inventory records. For instance, with real-time data on hand, companies can better avoid overstocking, which ties up capital unnecessarily, or understocking, which can lead to missed sales opportunities.
A practical cost-saving measure I've implemented involved adopting the Just-in-Time (JIT) inventory system in a manufacturing firm. By aligning inventory orders with production schedules, the company was able to significantly reduce the holding costs associated with storing excess materials. Additionally, we negotiated bulk purchase discounts with suppliers for key materials, ensuring lower purchase prices while still keeping inventory levels lean. These strategies not only saved on direct costs but also improved workspace efficiency by reducing the clutter of unused inventory. Managing your resources efficiently will always pay dividends, ensuring that operations run smoothly and cost-effectively.
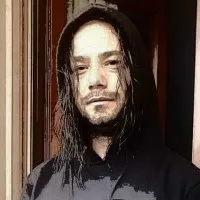
Data-Driven Forecasting Enhances Inventory Efficiency
Effective inventory management at DYNAMO LED DISPLAYS relies on real-time tracking and data analysis. One strategy we use is implementing a just-in-time (JIT) inventory system, which ensures we only order materials as they're needed for production. This approach minimizes overstocking, reduces storage costs, and limits the risk of obsolete inventory.
For example, by analyzing past sales data and current demand trends, we can accurately forecast inventory requirements, preventing unnecessary waste. Additionally, we use inventory management software to monitor stock levels and automate reordering processes. This not only improves efficiency but also allows us to focus on delivering high-quality products without interruptions. For any business, leveraging data and automation is key to optimizing inventory management and reducing waste.
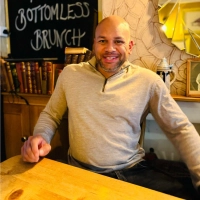
Cycle Counting Maintains Accuracy Without Disruption
Implementing cycle counting is a smart way to keep track of inventory in real-time. This method involves regularly counting a small portion of inventory, which helps maintain accuracy without disrupting daily operations. By doing this, businesses can spot discrepancies quickly and fix them before they become bigger problems.
Cycle counting also reduces the need for costly and time-consuming full inventory counts. This approach can lead to better inventory management and lower costs over time. Start implementing cycle counting today to improve your inventory accuracy and reduce expenses.
ABC Analysis Prioritizes High-Value Inventory Items
ABC analysis is a powerful tool for managing inventory more effectively. This method groups items into three categories based on their importance and value. By focusing more attention on high-value items, companies can better control costs and reduce waste.
ABC analysis helps businesses make smarter decisions about stock levels, reorder points, and storage locations. This approach can lead to significant cost savings and improved efficiency in inventory management. Begin using ABC analysis to prioritize your inventory control efforts and optimize your resources.
Vendor-Managed Inventory Reduces Overhead Costs
RFID technology offers a modern solution for tracking inventory automatically. By attaching small tags to items, businesses can monitor their movement and location in real-time. This technology reduces human error and speeds up the process of counting and locating inventory.
RFID can also help prevent theft and loss, leading to cost savings. Implementing RFID can improve accuracy and efficiency in warehouse operations. Consider adopting RFID technology to streamline your inventory tracking and reduce labor costs.
Cross-Docking Cuts Storage Expenses Significantly
Vendor-managed inventory is a collaborative approach that can greatly reduce overhead costs. In this system, suppliers take responsibility for maintaining agreed-upon inventory levels at their customers' locations. This arrangement can lead to lower carrying costs and reduced risk of stockouts.
Vendor-managed inventory also frees up time and resources for the business to focus on core activities. This strategy can improve supply chain efficiency and strengthen relationships with suppliers. Explore vendor-managed inventory options with your key suppliers to optimize your inventory management.
RFID Technology Automates Inventory Tracking
Cross-docking is an efficient logistics method that can significantly cut storage costs. This technique involves unloading materials from incoming trucks and loading them directly onto outbound trucks, with little or no storage in between. By reducing the need for warehousing, cross-docking can lower inventory holding costs and decrease the risk of damage to goods.
This approach also speeds up the delivery process, improving customer satisfaction. Cross-docking can be particularly effective for perishable goods or items in high demand. Investigate how cross-docking could be applied to your business to minimize storage expenses and improve product flow.